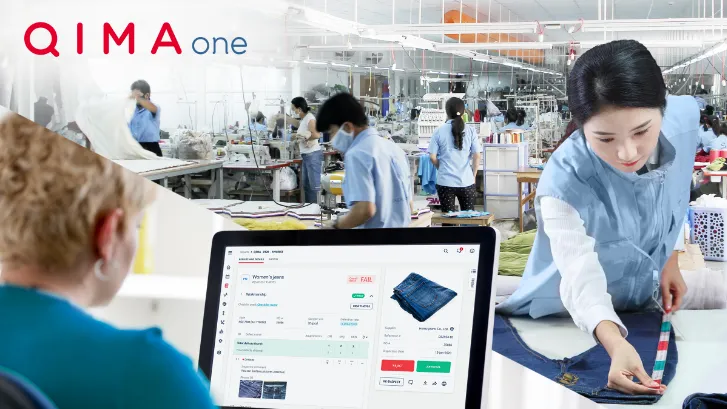
QIMAone: Quality and compliance under control with digitalization
The firm bagged the Software - Business Services award at HKB Technology Excellence Awards 2021.
Many businesses continue to implement quality control through pen and paper, spreadsheets, and emails. These methods, while working, have become time-consuming and often result in high defect rates and non-compliance.
In 2020, one of the TIC (testing, inspection, and certification) industry leaders, QIMA, raised the bar for quality control technology by launching QIMAone, a proprietary quality and compliance management software designed to digitize quality control processes and supplier management. The company understood the needs of its clients and took action immediately, translating to the platform's success today.
QIMAone has gained the trust of a number of large multinational and consumer goods brands. This further increased the platform's reliability and good reputation in the supply chain industry.
QIMAone equips businesses with tools to fix existing supply chain problems. The platform streamlines operations based on location, product expertise, risk, and the team’s schedules with automated inspection workflows. This results in standardized processes and data, ensuring consistency with suppliers. The QIMA Academy e-learning platform, including multiple industry-proven courses, is also integrated into QIMAone for new and existing suppliers.
Moreover, businesses can practice risk management with QIMAone’s AI risk radar and supply chain mapping capabilities. Risks are determined to prevent unethical sourcing and hazardous products. QIMAone also boosts the productivity of inspectors and reduces the risk of human error by accessing voice recognition technology when taking measurements.
The QIMAone platform is accessible from all devices. Therefore, inspectors can conduct inspections using a smartphone or tablet while management can review reports and make faster decisions. For better transparency, the embedded message center allows live chat communication between brands and suppliers, enabling them to identify and solve issues a lot faster.
QIMAone also goes beyond quality control management. The platform provides advanced data visualization so clients can follow quality trends and benchmark supplier performance by improving decision-making skills.
Ariat International, a US-based leading brand of innovative footwear and apparel, partnered with QIMA to deploy QIMAone in their operations. The digital platform increased Ariat’s supply chain visibility while improving quality control management. Overall, quality costs have been reduced for Ariat and the joint partnership has empowered Ariat to consistently be productive without sacrificing quality.
Beth Cross, chief executive officer at Ariat International, said that QIMAone is intuitive and easy to use. It allows the company to collect reliable data that provides a more precise view of the quality and compliance performance of the supply chain. It helps Ariat establish transparency and coordination, ensuring product quality and at the same time, reducing costs.
A team of dedicated inspectors, software developers, and experts in quality and compliance management are an integral part of the success of QIMA over the past 16 years. Through their collective effort, clients have saved up to 50% of inspection time and brought a significant reduction in margin of error in contrast to traditional means. Clients claim that quality issues are reduced by 32% after the software implementation due to consistently accurate standards and measurement.
This innovative solution led to QIMA’s win at the HKB Technology Excellence Awards.
Digitalisation is imminent and inevitable. Thanks to innovations like QIMAone, both executives and employees in quality control can take back their time and focus on developing the business.